Новая модель процессов литья плоских слитков позволит российским производителям алюминиевых полуфабрикатов для кораблестроения, космической отрасли и авиастроения снизить затраты.
Разработкой занимаются учёные Института цветных металлов СФУ: они предложили более эффективную модель процессов литья плоских слитков из экономнолегированного алюминиево-скандиевого сплава. Этот сплав, кстати, тоже разрабатывали ученые СФУ по заказу РУСАЛа: редкоземельный элемент скандий стали используют в составе сплавов на основе алюминия, чтобы придать изделиям особую прочность, износостойкость и долговечность.
Затраты скандия совсем невелики, но оказываемый им эффект позволяет применять такие сплавы в производстве деталей для автомобилей, судов, самолётов, в ракето- и спутникостроении и т. д. Эти сплавы ученые использовали в экспериментах для разработки оптимальных параметров литья слитков.
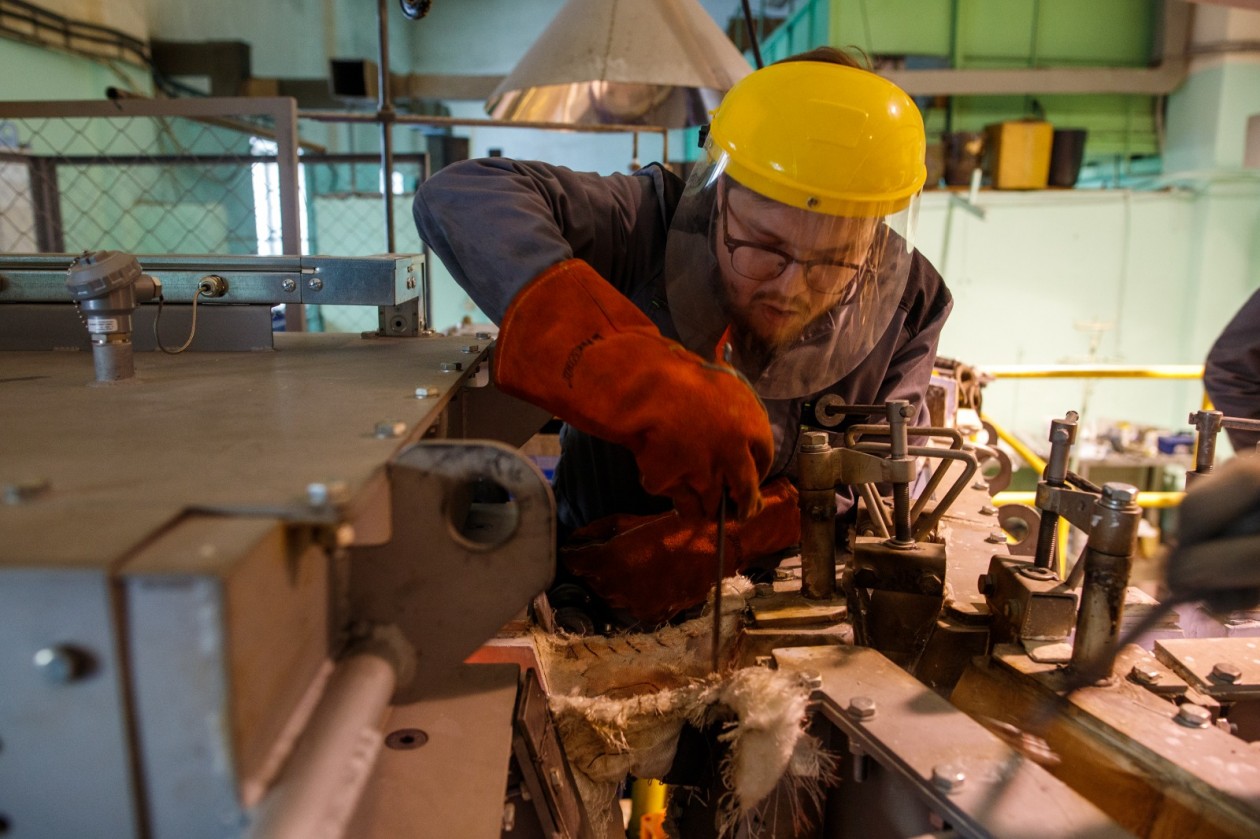
Как рассказали в пресс-службе вуза, эти параметры делают слитки более равномерными по структуре и составу. Это важно для последующих обработки и производства полуфабрикатов и их качества. Если слитки качественные, максимально однородные внутри, без точек напряжения и деформации, то процент брака на производствах в стратегически важных отраслях снизится. Изготовленные изделия будут более прочными и износостойкими и будут менее подверженны разрушению.
«Из-за некачественных слитков полуфабрикаты из них не получаются и приходится всё переделывать, это провоцирует рост затрат на производство. Наша модель такие затраты минимизирует», — рассказал ведущий научный сотрудник лаборатории физикохимии металлургических процессов и материалов СФУ Александр Безруких.
По словам Безруких, на металлургических производствах, конечно, контролируют качество слитков, но делают это на отдельных фрагментах — для исследования берутся поперечные образцы слитка (темплеты) толщиной не более 150 мм. Длина же плоских слитков может достигать в продольном направлении до 6–10 метров, при этом выявить возможные скрытые дефекты «сердцевины» слитка не всегда возможно.
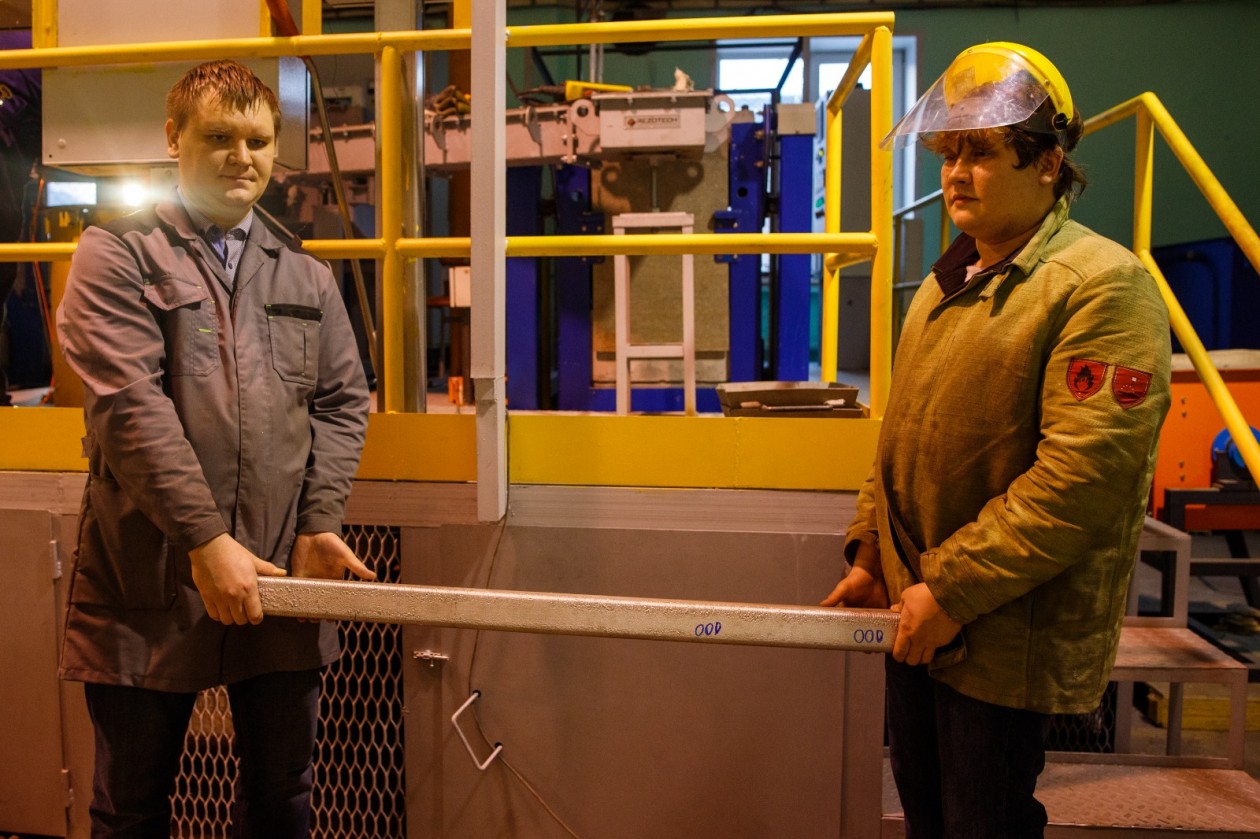
Визуально бракованные слитки со скрытыми внутренними дефектами (такими, например, как внутренние трещины и микротрещины, скрытые в теле слитка) могут не отличаться от качественных. Производитель может квалифицировать их как годные. Дефекты обнаружат уже при последующей обработке в процессе прессования или прокатки.
«Если заранее с помощью моделирования подобрать технологические параметры производства, весь слиток получится однородным, без неприятных „находок“ в сердцевине», — поясняет Безруких.
Ученые проводили эксперименты на лабораторной установке непрерывного литья, которая представляет собой мини-заводской цех в Институте цветных металлов СФУ. Они отливали слитки из алюминий-скандиевого сплава, замеряли нужные температурно-скоростные параметры и интерполировали их в математическую модель. Все корректировки, полученные в ходе реального эксперимента, вносились в математическую модель в программе ProCAST — так была получена оптимальная модель кристаллизации слитка.
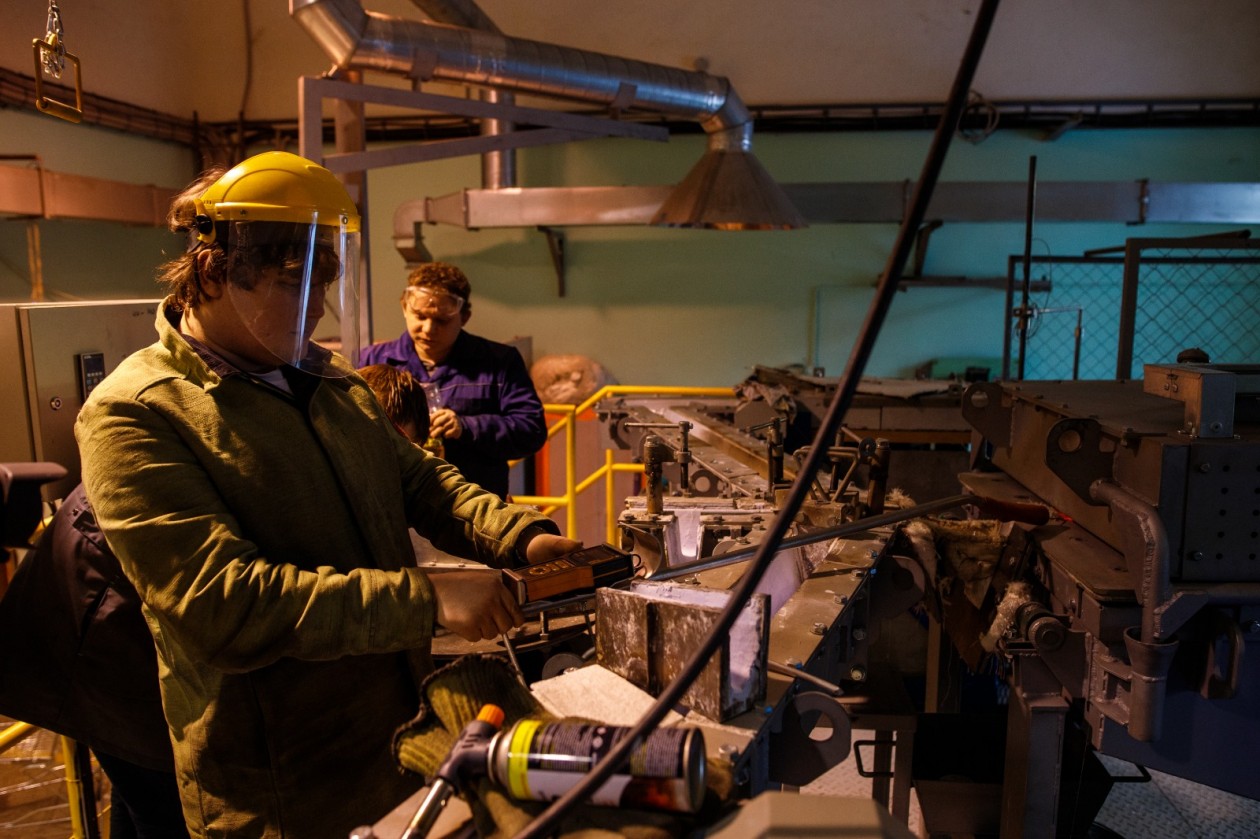
Разработанную методику смогут использовать для достоверных результатов моделирования литья слитков из алюминиевых сплавов схожего состава, в том числе легированных другими редкоземельными элементами в комплексе со скандием. Полученную модель характеризуют высокой сходимостью результатов и низкой погрешностью: по мнению ученых, ее использование внесёт свой вклад в развитие металлургической промышленности и технологический суверенитет нашей страны.
Сейчас ученые проводят испытания новой модели на алюминиевых сплавах с другими редкоземельными и переходными металлами.
Фото: news.sfu-kras.ru
Lx: 3653